High-temperature industrial environments, such as glass furnaces, steelworks or incinerators, pose extreme challenges for monitoring and inspection. To guarantee safe, reliable performance, industrial endoscopes need to be designed with materials and systems capable of withstanding temperatures of up to 2000°C. Why 2000°C? Because, quite simply, we’ve never had the opportunity to test hotter!
In industrial furnaces and incinerators, temperatures regularly exceed 1000°C. These conditions lead to :
Accelerated wear and tear on equipment exposed to heat.
Accumulation of dust and corrosive gases, reducing component durability.
Structural constraints, particularly in localized hot spots.
The choice of materials for high temperatures
- 316L stainless steel: Its high chromium content forms a passive chromium oxide layer that protects the alloy against oxidation and corrosion. Molybdenum enhances its resistance to chlorinated and acidic environments, while nickel stabilizes the austenitic structure, providing excellent mechanical strength at high temperatures. It can withstand temperatures of up to 925°C in intermittent service without cooling, while maintaining its structure and durability.
- Hastelloy: A nickel-based alloy, Hastelloy is renowned for its exceptional resistance to highly corrosive environments, particularly in the presence of strong acids and high temperatures. Its molybdenum- and chromium-rich composition gives it excellent chemical stability and enhanced resistance to oxidation, even under extreme conditions.
- Arcap: Composed mainly of nickel and copper, Arcap is naturally resistant to oxidation and aggressive environments, without the need for surface treatment. Unlike steels, it does not undergo embrittlement due to thermal aging.
Air cooling: the Venturi effect
Air cooling is based on the Venturi effect, a physical phenomenon that occurs when a fluid (air in this case) passes through a narrowed duct.
Principle:
As air passes through a constricted passage, its velocity increases while its pressure decreases. This rapid airflow is used to ventilate the front lens of endoscopes, preventing excessive heat and particle deposits (dust, ash).
Advantages :
Prevents lens overheating by maintaining a constant, rapid flow.
Prevents the build-up of solid residues on the lens, ensuring optimum visibility.
Simple, effective solution for dusty or closed environments.
Water cooling: efficient and robust
The water-cooling system is based on the superior thermal properties of water, which conducts heat around 30 times faster than air.
Principle:
An internal circuit circulates water through a stainless steel cooling jacket.
This circulation rapidly dissipates the heat accumulated on surfaces exposed to high temperatures.
The sheath is often designed with a helix structure (Vortex effect) to distribute the water evenly over the entire cooling surface.
Advantages:
Significant reduction in hot spots, extending component life.
Ability to maintain a stable temperature even in environments exceeding 1500°C.
Ability to operate at higher speeds, optimizing performance while reducing system noise.
The role of the triple sheath
In high-temperature industrial environments, endoscope protection is essential to guarantee longevity and performance. The triple-envelope sheath meets these needs by offering advanced thermal protection.
Multi-layer design:
The sheath is composed of three distinct layers, each with a specific function to insulate and protect internal components
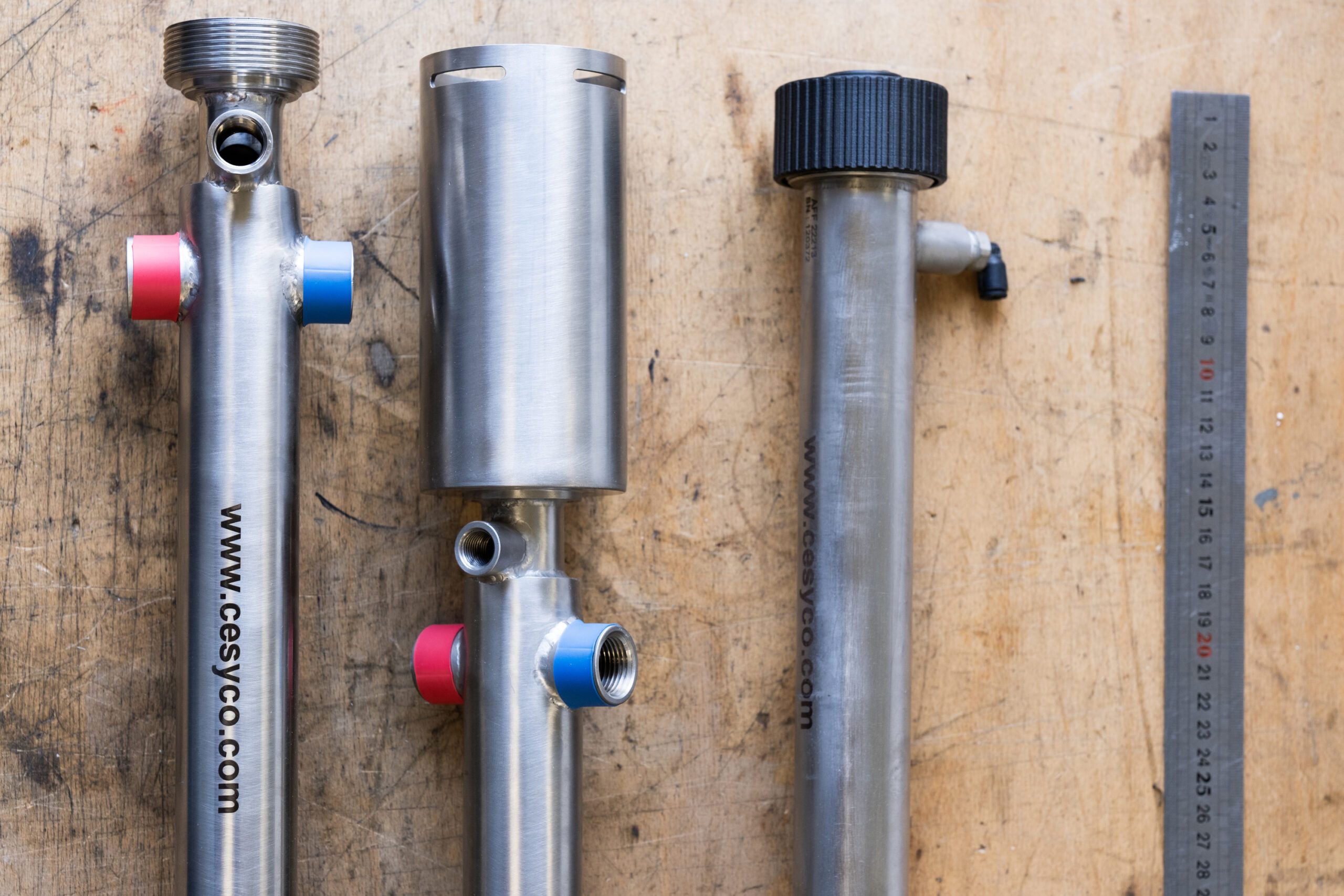
The role of the triple sheath
In high-temperature industrial environments, endoscope protection is essential to guarantee longevity and performance. The triple-envelope sheath meets these needs by offering advanced thermal protection.
Multi-layer design:
The sheath is composed of three distinct layers, each with a specific function to insulate and protect internal components.
Integrated cooling circulation:
Water: The first layer incorporates a water cooling system, effectively dissipating heat from the environment.
Air: An additional layer optimizes air flow to protect the front lens and prevent particle build-up.
Insulation: The outer layer provides an additional barrier against extreme temperatures and corrosive conditions.
Specific benefits:
Enhanced thermal resistance: Able to operate reliably at temperatures close to 2000°C.
Component preservation: Significantly reduced thermal stress on the internal parts of the endoscope, ensuring optimum durability.
Enhanced safety: Multi-layer design minimizes the risk of failure, even in the most demanding environments.
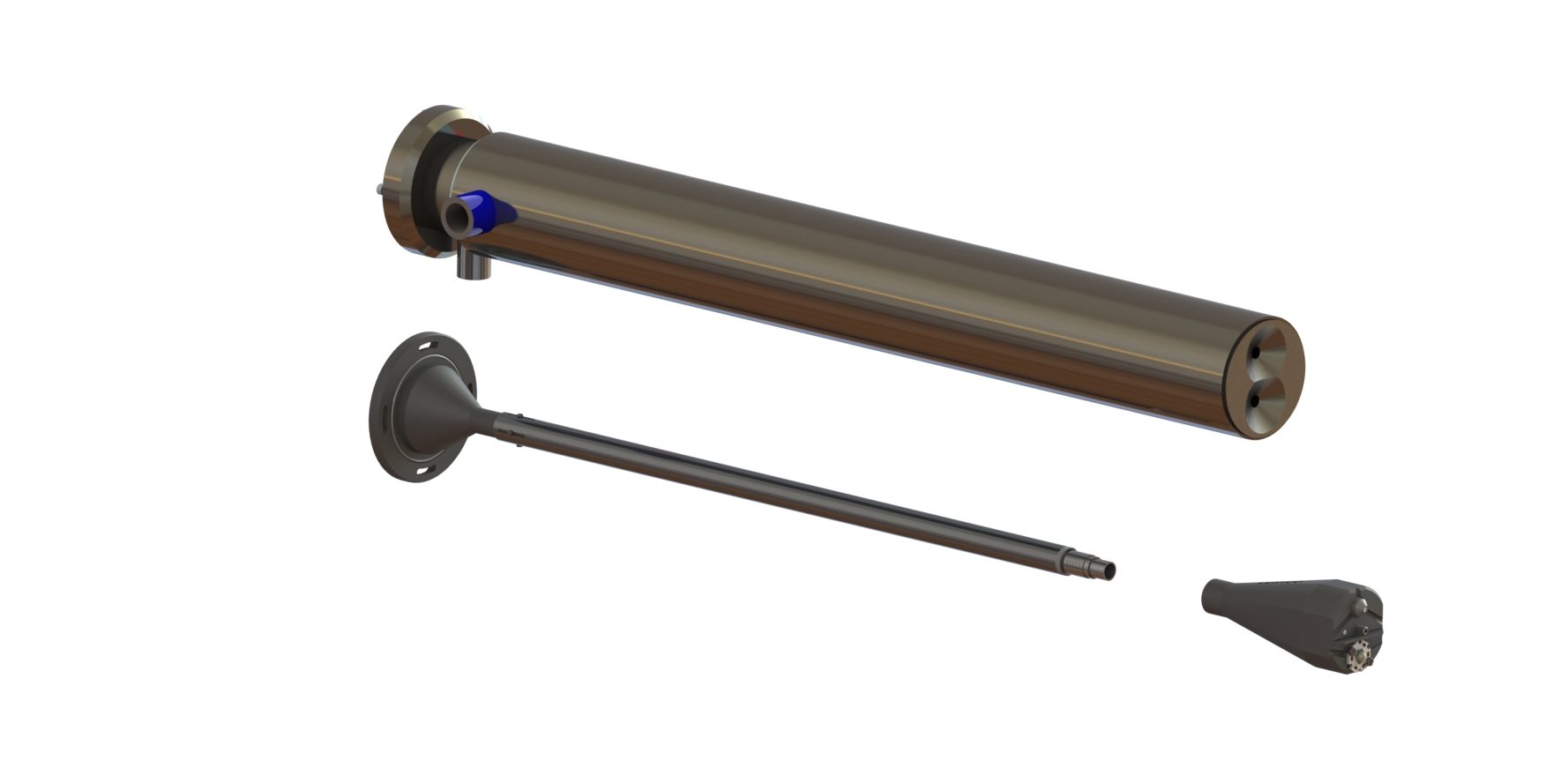
Pour conclure :
Thanks to the triple-envelope sheath, combined with air and water cooling systems, Cesyco endoscopes offer a complete solution for high-temperature inspection. These innovations enable :
- Maximum protection of critical components.
- Reduced need for costly maintenance.
- Improved overall equipment performance, even in environments where heat and corrosion are omnipresent.
Resistance to 2000°C is not just a requirement, it’s a promise that Cesyco keeps thanks to its choice of materials and proven technologies. The use of 316L stainless steel, combined with advanced cooling systems and state-of-the-art image transmission, guarantees the reliability and durability of our endoscopes in the most extreme environments. With the integration of triple-envelope sheathing and advanced cooling technologies, Cesyco is pushing back the boundaries of industrial endoscopy. These solutions guarantee enhanced safety, exceptional durability and uncompromising performance, enabling industries to meet the challenges of the most extreme environments.
Ready to discover our solutions? Contact us to find out more!